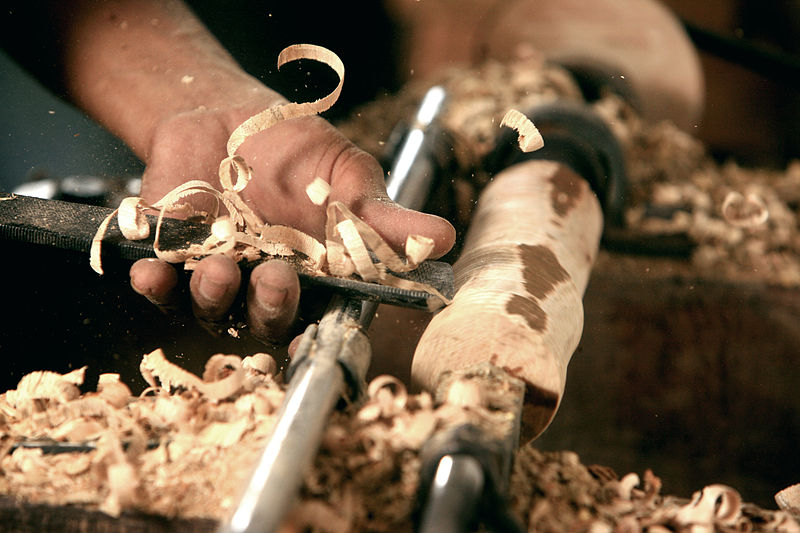
Chattahoochee Woodturners collaborated with Eagle Ranch in order to build a woodturning room on their school campus. The American Association of Woodturners provided an Educational Opportunity Grant and donated other funds to help build the facility. Local woodturners donated equipment as well as tools to help get this project off the ground. Woodturning classes are open to all students. There is also a woodshop for adults with handicaps.
Hark Woodturner
Hark, a resident tutor, approached Hark eight years ago after a class. Hark agreed to teach the Harvard class. After several failed attempts at teaching the course at Harvard he finally found a used lathe in the basement from a neighboring building. He began his first Harvard class that spring. Today, students from all Harvard Houses are welcome to attend the woodturning studio's classes, and he continues to teach woodturning on the weekends.
Arthur and Pamela are not only teachers, but also travel to trade shows and woodworking symposiums in search of new audiences. They have hosted guests from many world-famous artists and met them. Woodturning workshops featured many artists from all walks of life. The studio has also sent a Commander and Knight to the Norwegian Woodturning Cruise which is held every three-years.
Tools
One of the most important items to have in your woodturning studio is safety gear. To keep the glare from sand on your face, you might want to purchase safety glasses, eye protection, or a visor. To keep your tools in tip-top shape, you can also invest in sharpening equipment. In addition to safety gear, you'll want to invest in a jigsaw or lathe to sharpen the lathe blades.
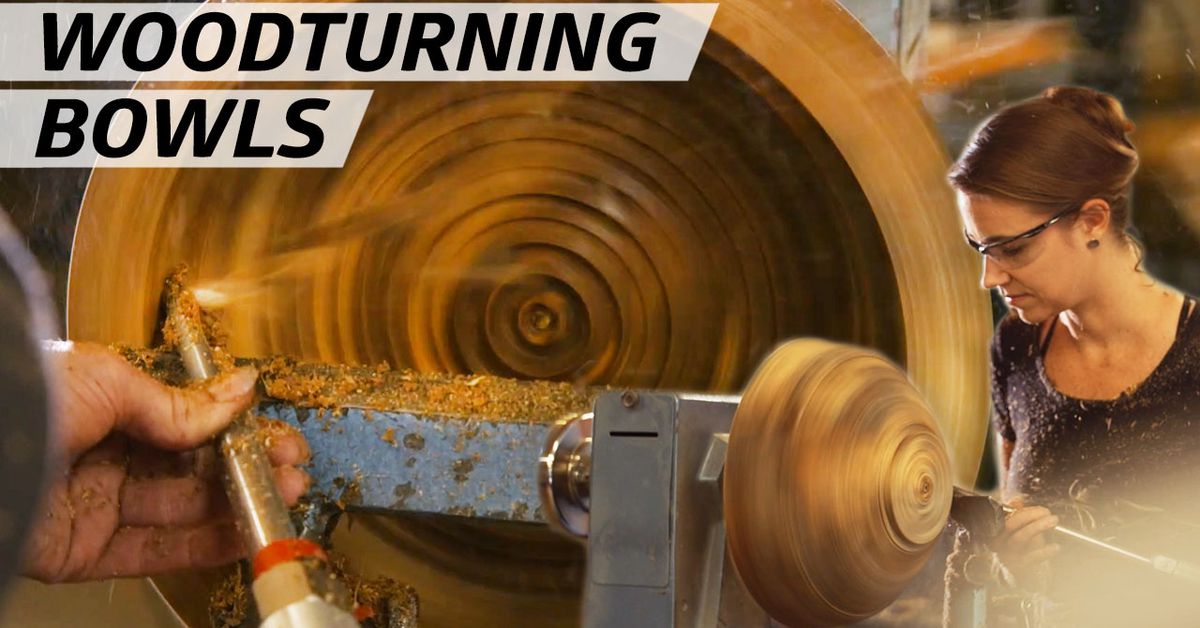
A drill, a wrench, and a banjo are three of the most important tools you will ever need. The banjo lets you slide your tool along the lathe bed supporting the toolrest. This allows you to hold the turning tool in the most convenient location. While the banjo can be adjusted, most modern lathes feature a locking mechanism. These tools will be necessary for creating your own unique creations.
Techniques
You should be able to use the right tools and techniques whether you are woodturning for hobby purposes or as a professional. These tools will allow you to create beautiful functional pieces that will look great and be useful. These tools can be purchased online, or in a local woodworking workshop. Wood turning is a time-consuming process, but the results can be well worth it.
If you are just beginning, a woodturning workshop is a great place to start. The workshop covers everything, from safety gear to selecting the right tools and techniques. You will also get hands-on experience using a lathe. It will be a hands-on experience to learn tools properly and to apply the techniques to your own work. Your projects can vary depending on the skills that you have, from making bowls and bottle stoppers to carving mallets.
Class size
A beginner's workshop in Durham, NC is a great way to learn the basics of woodturning. This class will teach you basic techniques, how to sharpen tools and how to use them. The class will also include several projects. Safety will be the focus of this class. Make sure you bring a helmet and protective gear.
It will allow you to put your focus on each student and their learning. Instructors will have plenty to respond to questions and provide individual attention. You can expect to learn at your own pace as there are usually only six students in each class. Most of the classes are project-based. Classes will typically last for two days. Private lessons can focus more on advanced techniques for those who are more skilled.
Cost
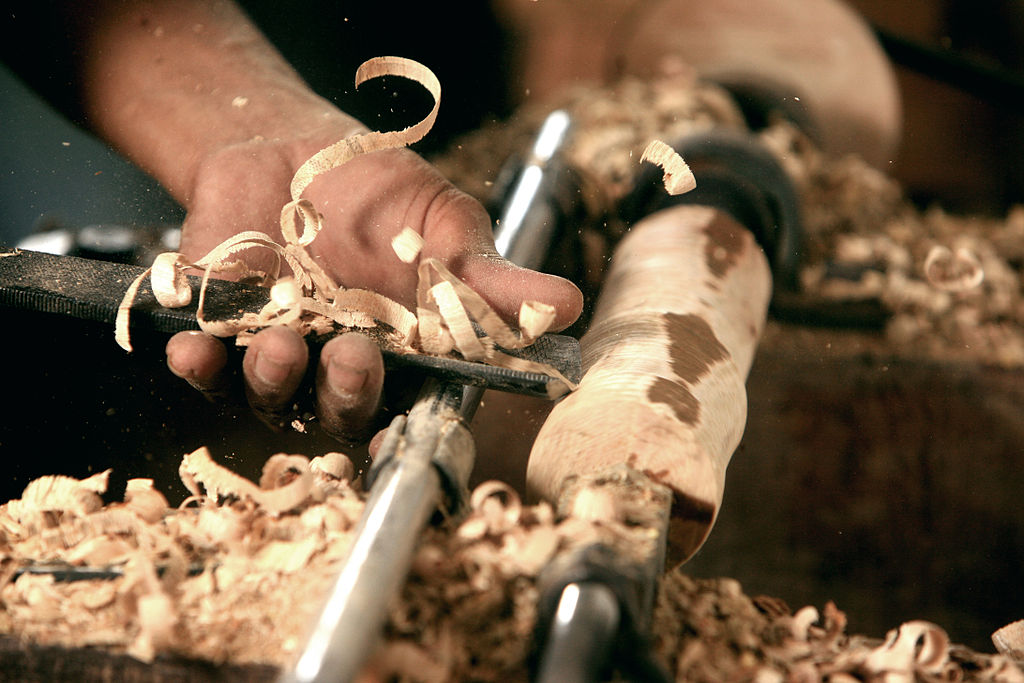
It will cost a lot to set up your own woodturning workshop. Equipment and supplies can easily cost several thousand dollars. A good way to save on these expenses is to sell your finished products for a reasonable price. Selling your finished products can increase your profits by up to three times. Although high-end products are a great way of promoting your art and generating profits, it's also possible to sell items at lower prices. Even though higher-end items take more time to produce, it is possible to sell simple items at this price range. They can even sell out in the first day of an art show that lasts two days.
If you are new to woodturning, a class will teach you the basics of the art. This will cover safe tool use and proper sharpening. This will allow you to move on to more difficult projects and teach you more advanced tools and techniques. A typical cost for an introductory class in woodturning is $75 for Mather residents and Harvard associates. All materials and tools included in the cost. A list of nearby hotels will be included.
FAQ
What kind and type of wood should i use?
Woodworking is a popular job that involves oak, pine and maple. Every type of wood is different and can have a unique look and feel that will affect the final product. Oak is a darker wood and tends to be more durable than other types. Birch, which is lighter and soft, is more heavy than mahogany. There are two options: solid wood and veneers. Veneers are thin sheets of wood that are glued together to form a single layer.
Do I have the potential to make a decent living doing this?
Yes! Many woodworkers do. According to U.S. Bureau of Labor Statistics (BLS), woodworkers earned a median annual salary of $34,000 in May 2012. This is significantly higher than the national average, which is $31,000 per year.
Where do I get my woodworking supplies?
There are many places where you will find everything that you need. You could also visit hardware stores in your area or shop online at Amazon.com.
You might also consider flea markets and garage sale for any old furniture or other materials you could reuse.
Are there any tips for starting a woodworking enterprise?
It can be difficult to start a woodworking shop. You won't mind working hard if your hobby is something you love. Plus, you'll probably enjoy the challenge of running your own business.
One thing to keep in mind when launching a new venture is that you might encounter unexpected problems along the way. Unexpectedly, money might run out. You might find customers not willing to pay the amount you expected. You must be ready to deal with such situations in order to survive.
It is a good idea to create a separate bank account just for your company. You'll know exactly how much money is coming in by setting up a separate bank account.
What is the difference between a hobbyist woodworker and a professional woodworker.
Hobbyists are passionate about making things from wood, while professionals tend to be more focused on the quality and craftsmanship of their work. Hobbyists take great pride in their creations, and share them with family and friends. Professionals will spend hours researching designs before they begin working on a project. They will meticulously plan every detail of their work from choosing the right materials to finishing it.
How much does a hobbyist need to invest in getting started?
You will need capital to purchase the tools and supplies you need to start your woodworking business. Start by getting a small circular saw saw, drill press or circular saw. These items are affordable so you won’t break the bank.
Statistics
- In 2014, there were just over 237,000 jobs for all woodworkers, with other wood product manufacturing employing 23 percent; wood kitchen cabinets and countertop manufacturing employing 21 percent. (theartcareerproject.com)
- The U.S. Bureau of Labor Statistics (BLS) estimates that the number of jobs for woodworkers will decline by 4% between 2019 and 2029. (indeed.com)
- The best-paid 10 percent make $76,000, while the lowest-paid 10 percent make $34,000. (zippia.com)
- Woodworkers on the lower end of that spectrum, the bottom 10% to be exact, make roughly $24,000 a year, while the top 10% makes $108,000. (zippia.com)
External Links
How To
How to stain wooden surfaces
Staining wood is the process of applying chemicals to the wood's exterior, which alters its color. This chemical reaction changes the wood's color from white to brownish. Although oak is the most popular type of wood to stain, there are many other types that can be used.
There are many methods to apply stain to wood surfaces. Mixing the stain in a solvent such as turpentine and spraying it onto the wood is one method. Other methods use a solution of water and dye applied directly to the wood. The stain can be mixed with paints and varnishes to become part of the final coating.
Preparing the wood surface is the first step to staining it. The wood must be thoroughly cleaned to remove all grease and dirt. Sanding the wood smooths out rough spots and scratches. The next step is to choose the stain type you want. Penetrating stains are different from non-penetrating. Penetrating stain penetrates deeper into wood than nonpenetrating, making them suitable for dark colors like mahogany. Light colors such as maple work well with non-penetrating stain.
Once you have decided on the stain type that you want, get your tools ready. Paintbrushes are great for applying stain because they allow you to evenly spread the liquid across the surface. To remove any stains left behind after painting, you will need some rags. If you are planning to mix your stain, ensure you have enough containers for each component.
Once you have prepared all your materials, it is time to clean the areas where you will stain the wood. You can remove grime and dirt with warm water and soap. Wipe down all furniture pieces with a dampened cloth and clean water. Be sure to get rid of all loose material, especially if staining is planned for darker wood.
The stain should be applied next. Next, apply the stain to the furniture by starting at one end. Slowly and carefully work your way along the grain to reach the opposite end. Make sure that the stain does not drip off the edge of the wood. Before proceeding to the next step, let the stain dry thoroughly.
Protect the painted surface with a coat polyurethane paint sealant. Three coats of polyurethane sealing agent are required. Allow the third coat of polyurethane sealer to dry overnight before applying the final coat.