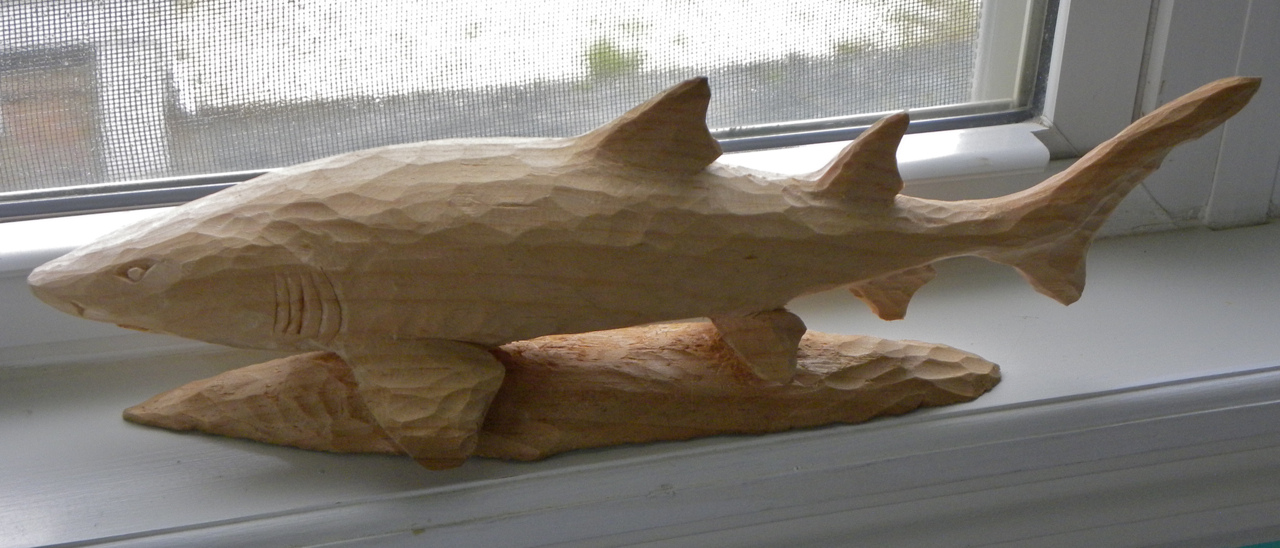
You need to be able to identify the wood species and what you should look for when carving a chain. You have many options for patterns and variations. Here are some tips to get you started. Learn how to make a chain and you can start carving your own. Follow these steps to make a beautiful, personal chain! You will be pleased with the results! Your chain will be a treasured memento!
Techniques
A chain can be used to decorate or as a gift wrap. First, choose a square-shaped piece of wood for carving. Basswood is recommended for beginners, but you can also use pine wood if you are a more experienced carver. Pine wood is easier to work with, but it will frustrate you until you get more familiar with this material.
A woodcarving magazine can provide a wealth of information for those interested in learning the art. Each article is written step-by -step by an accomplished author. These informative articles are written by experts and will walk you through every step of carving, from drawing your design to finishing it. Woodcarving makes a great hobby, especially for children. These guides can be used for anyone starting woodcarving, whether it's a child's first project of an adult.
Wood species
You have many options when it comes to carving a chain. Some species are more challenging than others. If you are looking for intricate designs, hardwoods might be a good option. These species are also readily available in large quantities, and they are less likely burn or char. Before carving, check out the Janka hardness rating. You can find this information on Bell Forest Products or Wikipedia.
Use a sharp saw or wood carving blade to create a chain out of wood. You will get a cross, not a square. Although it's possible to create any shape you want, the most effective wood chain is one with a single shape. Although you can make a chain in many different shapes it's better to start with one. It is also important that the wood is free from mud, bark, and other substances that can cause the chain's to crack.
Patterns
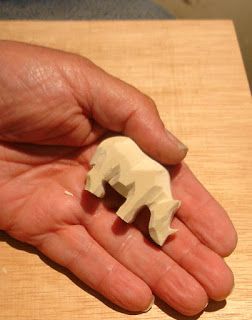
There are many different types of wood carving. Chain work is one of my favorite woodworking techniques. The sample to the right shows a one-piece woodcarving with a shackle. It also includes a four-foot long chain and 4" diameter balls. Each link's size and shape is determined by the chain pattern's grid. A scrollsaw is required to create a chain from a grid.
To carve a chain pattern, the first step is to hollow out the inside of the links. This allows you create the exact shape and size you need. Once you have established the basic shape, it is possible to refine the form of the chain links or create individual profiles. Chain patterns come in many shapes: they can be round, square, or oval. Beginners should stick to the round profile. For a more decorative and functional design, you can carve an octagon (or a diamond) into your chain.
Variations
There are many ways to carve a chain. One of them is carving the link's profile differently. By carefully carving the inside of your links, you can make your chain square- or cross-shaped. If you are a beginner, you may want to stick to carving a single shape. You can try other shapes to enhance your chain carving skills. Here are some of the more common varieties.
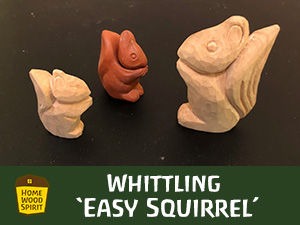
To carve a chains, you can use a knife or a strong-nosed chisel. This is done using the same principle as carving decorative wooden vessels. A long bar is cut into a ring handle, spider, or links. This type of carving requires patience and practice because one wrong move can break the chain. You should also select a manager with the appropriate profile depending on what the chain will be used for.
FAQ
How can I keep my shop organized?
To keep your workshop tidy and organized, you should first create a place for tools storage. To keep your tools sharp and ready for work, keep them clean of dust and debris. You can hang tools and accessories with pegboard hooks.
Where can I locate free woodworking plans
Woodworking plans can be found online without the need to purchase books or magazines. Just search Google. Simply type "free woodworking” into the search box and you'll find hundreds of websites that offer free plans.
What kinds of woods are good for making furniture?
Woods are classified according to their hardness. Softwoods can be pine, fir or cedar. Because they resist rot, softwoods can be used to make outdoor furniture. The hardwoods include teak, maple, mahogany and oak. They're generally used indoors because they won't weather well outdoors.
What kind of wood should I use?
The most commonly used woods for woodworking are oak, maple, cherry. Each type of wood has unique characteristics that affect the look and feel of the final product. Oak, for instance, is darker and harder than most other woods. Birch is lightweight and soft while mahogany is heavier and denser. There are two options: solid wood and veneers. Veneers can be described as thin sheets of wood that have been glued together in one layer.
What is the hourly rate for a woodworker?
The hourly rate for a professional woodworker varies depending on many factors, including skill level, experience, availability, location, and other variables.
An hourly wage for skilled woodworkers is between $20 and $50.
A less experienced woodworker may charge as little as $10 an hour.
How do I know what type of wood I'm dealing with?
Always inspect the label when buying wood. The label should detail the wood species, its moisture content and whether it has been treated or not.
Statistics
- Woodworkers on the lower end of that spectrum, the bottom 10% to be exact, make roughly $24,000 a year, while the top 10% makes $108,000. (zippia.com)
- Average lumber prices rose about 600 percent between April 2020 and May 2021. (familyhandyman.com)
- Overall employment of woodworkers is projected to grow 8 percent from 2020 to 2030, about as fast as the average for all occupations. (bls.gov)
- If your lumber isn't as dry as you would like when you purchase it (over 22% in Glen Huey's opinion…probably over 10-15% in my opinion), then it's a good idea to let it acclimate to your workshop for a couple of weeks. (woodandshop.com)
External Links
How To
How to join hardwood without using nails
Many people love woodworking. It's fun and relaxing because you can use your hands to make something useful from wood. You may need to join two pieces without the use of nails. This article will help you to maintain the beauty of your woodwork projects.
Before joining the pieces of wood together, you will need to first trim any edges. Avoid leaving sharp edges that could lead to problems later. After you have completed this step, you are ready to glue your boards together.
If you are working with hardwood, only one side should be glue. For softwoods like cedar and pine, glue should be applied to both sides. After applying the glue, press the boards firmly until they are completely stuck together. Before moving onto the next step, make sure the glue has dried completely.
Once you've glued your boards together you will need to drill holes in the joints to accommodate screws. Depending on what type screw you choose, the size of these holes will depend on how big they are. If you are going to use a half-inch wood screw, you will need to drill at least 3/4 inch deep.
After drilling the holes, you can drive the screws into your board's backside. Don't hit the board's surface. You could damage the finish. Don't drive the screws too far into the end. This will help prevent splitting of the end grain.
Once your project is complete, it's time to protect it against the elements. You can seal the furniture pieces or cover the top. It doesn't matter what method you use, you want something that will last many years. There are many options: oil-based varnishes; polyurethane; shellac; lacquer.
These products can usually be found at any home improvement store. It is important to ensure that you purchase the correct product for the job. Don't forget to keep in mind that some finishes are toxic. Wear protective gear whenever you are handling them.