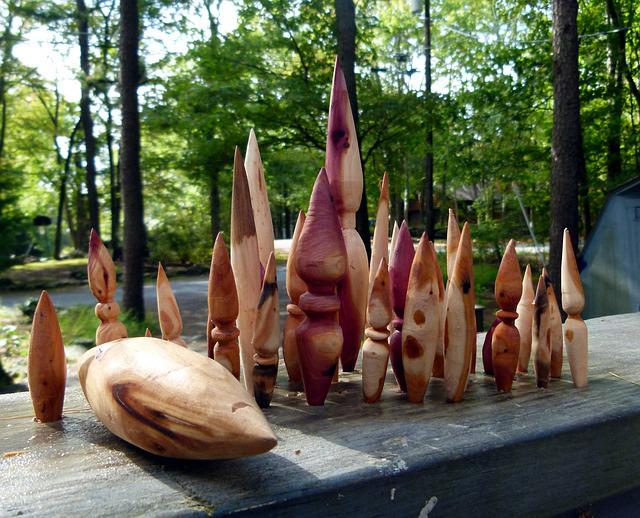
A digital caliper will help you measure the thickness of your pieces. You can make your own calipers by dismantling one and silver soldering a set of jaws to it. In this article, you will learn how to make a set of spring calipers. You can also change the thickness of the jaws of a digital caliper. You can also make your own wood turning tools once you are familiar with how to use a digital calculator.
Dismantling the digital caliper
If you're a woodworker, then you might be curious how to take apart a digital woodturning caliper. While these calipers are a great tool for making precise measurements, they can be tricky to dismantle. These are some steps:
Set of jaws made from silver soldering
When soldering jaws together, ensure that they are at least 25 degrees. Make sure you are velling the blade sides. You can see the entire process in the image below. The next step is to cut the ribbon silver solder to your desired length.
Make a set spring calipers
It is possible to make a set spring calipers. You can actually make a set of these spring calipers in just an hour. The divider is a useful tool for measuring the diameters and wall thicknesses of turned vessels. The divider has two straight adjustable legs, each with sharp points at one end. The divider measures approximately half the height as a male. A firm-joint caliper is held in place by friction on the joint. Inside calipers measure the diameter of a hole, and they are useful for measuring the distance between two surfaces.
Adjusting the thickness for the jaws with a digital caliper
One of the most important tools to use when woodworking is a caliper. These calipers measure both the internal and exterior dimensions of a piece. The calipers also include a depth gauge, which measures the distance between objects. There are several parts to a caliper, including an exterior jaw and a depth indicator. You will need a caliper with an exterior jaw and a depth gauge for wood turning.
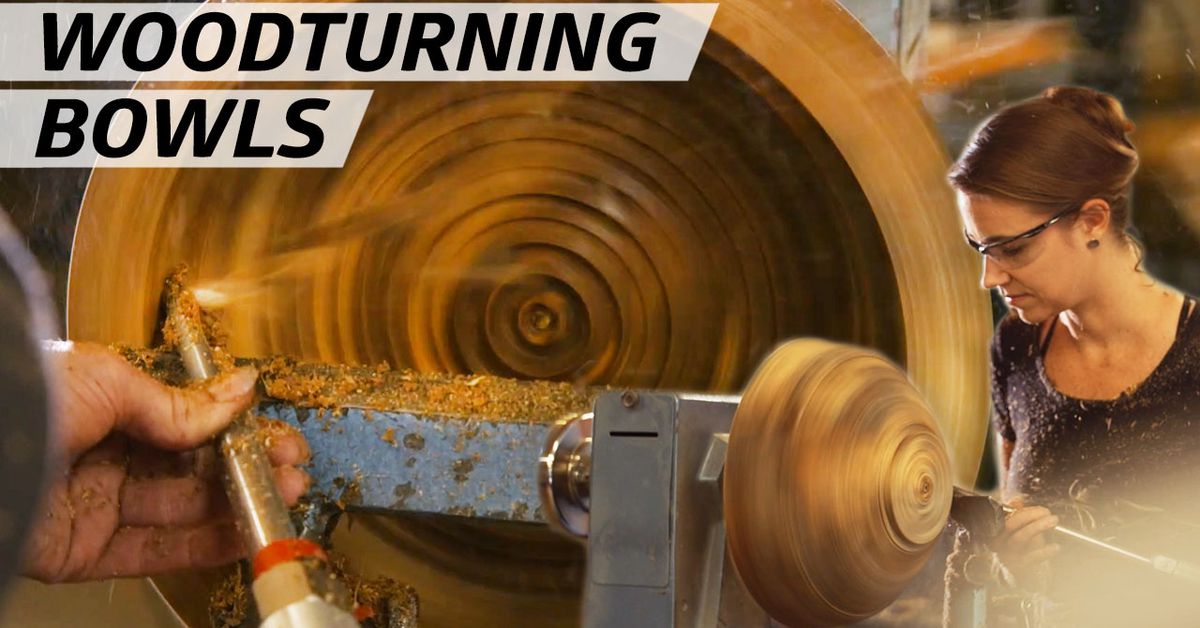
Use a digital caliper to measure distances. One of the most difficult measurements is achieving a precise and consistent reading. It is difficult to hold your caliper perpendicularly on the face you are measuring. This can lead to multiple measurements that may be necessary to obtain an accurate reading. Different machinists might get different depth measurements. The digital caliper can measure both external and internal diameters.
Galbert calipers
Galbert woodturning calipers may be an excellent time-saver when turning a 10on. These calipers allow you to measure the diameter of your work without having to stop the lathe. The caliper simply fits on the work and cuts until it reaches its target diameter. I found that this tool cut down on my tenon-turning process by half. The best thing about this tool is that it can be used for a number of projects.
Galbert wood-turning tools are easy to use. It makes repetitive pieces more accurate and consistent. It has a built-in metering scale, and allows you to accurately measure the diameter as you cut. This tool can be combined with a dividing tool to allow you to quickly alter the diameter of your piece. It's also easy to use, and you can use it for measurements of the spindle diameter.
FAQ
What is the hourly rate for a woodworker?
The hourly rate for a professional Woodworker will vary depending on many variables, such as experience, skill level and availability.
The average hourly rate for a skilled woodworker ranges from $20-$50 an hour.
A less skilled woodworker might charge as low as $10 per hour.
How long does it take to finish a piece of furniture?
It depends on the size of the piece of furniture. A smaller project like picture frames or boxes can be completed in a single day. Larger projects, like desks or dining tables require several days. It takes time and effort to properly stain the wood.
How much does a hobbyist need to invest in getting started?
You will need capital to purchase the tools and supplies you need to start your woodworking business. The best place to start is by buying a small drill press, circularsaw, circular saw or sanding machine. These items don't cost much so they won't break your budget.
Does it take a genius to make woodworking work?
No. Woodworking is not rocket science. You can create beautiful pieces of art by learning how to use simple power tools.
Statistics
- Overall employment of woodworkers is projected to grow 8 percent from 2020 to 2030, about as fast as the average for all occupations. (bls.gov)
- The U.S. Bureau of Labor Statistics (BLS) estimates that the number of jobs for woodworkers will decline by 4% between 2019 and 2029. (indeed.com)
- In 2014, there were just over 237,000 jobs for all woodworkers, with other wood product manufacturing employing 23 percent; wood kitchen cabinets and countertop manufacturing employing 21 percent. (theartcareerproject.com)
- Woodworkers on the lower end of that spectrum, the bottom 10% to be exact, make roughly $24,000 a year, while the top 10% makes $108,000. (zippia.com)
External Links
How To
How to join wood with no nails
Woodworking is a popular hobby. Woodworking can be a fun hobby because you can work with your hands to make useful objects from wood. You might want to join two pieces from the same wood, but you don't need to use nails. This article will explain how to do this so that your woodwork projects stay beautiful.
First, remove any sharp edges from the wood pieces before you join them. You don't want to leave sharp corners that could cause problems later on down the road. Now you can start gluing the boards together.
If you're working with hardwood, you should only apply glue to one side. You should glue both sides if you are working with softwoods such as pine and cedar. Once the glue has dried, press the boards together until they are fully adhered. Before you proceed to the next step, be sure to let the glue dry completely.
Once you've glued your boards together you will need to drill holes in the joints to accommodate screws. The size of these holes depends on what type of screw you choose to use. For example, if your screw is a 1/2-inch wooden screw, drill a hole that is at minimum 3/4 inches deep.
Once you've drilled your holes, you'll want to drive the screws through the joint and into the backside of the board. You should be careful not to touch the board's front surface. This could cause damage. Be careful not to drive the screws too hard at the ends. This will prevent the wood from splitting.
Once your project is complete, it's time to protect it against the elements. You can either cover the entire furniture or just the top. You'll want a product that lasts for many years. Some examples include oil-based varnishes, polyurethane, shellac, lacquer, etc.
These products can generally be found in any home improvement shop. Be sure to choose the right one for your project. Don't forget to keep in mind that some finishes are toxic. Always wear protective gear when handling any of these finishes.