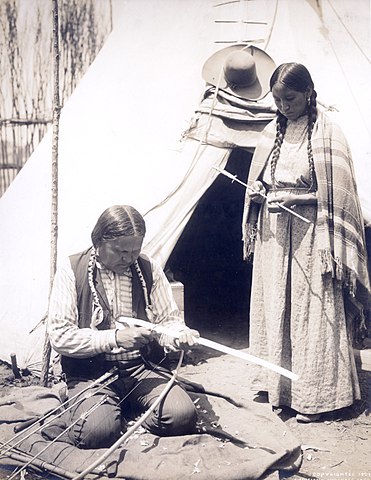
There are several things you should keep in mind when looking for an oar-carving knife. When purchasing a knife for carving, size, sharpness as well as stag bone and lamination are all important factors to consider. Learn how to choose the best one for you. After reading this article, you'll have an idea of what to look for when purchasing your new oar carving knife.
Size
The Oar Carver series of carving pocket knives is a classic and epitome of this craft. Three sizes are available in the current lineup. Version 2 is larger, with a thinner blade. Version 3 features a thicker edge and a wider gap. Here are some tips to help choose the right size.
Sharpness
The edge of your oar carver knife is an essential aspect. You should keep your knife's edge sharp. Your knife will begin to show signs of wear like chips, dullness and nicks. Luckily, it is relatively easy to gauge the sharpness of an oar carving knife by observing the edge. A magic marker can help you match the angle of each knife's edge to the blade's center.
A way to check the sharpness and quality of an oar carver knife is to cross a piece of basswood along its end grain. The blade should cut through the wood with no drag marks or ripples. A smooth cut is like cutting a baby's bottom without leaving any marks. If you see any of these marks on the blade, it might not be sharp enough to use for carving. It is important to regularly check the sharpness a oar-carving knife.
Laminated blades
The Oar Carver series, created by Ross Oar, a world-renowned knifemaker, is a classic example for the carving pocketknife. There are currently three versions: Versions 1 through 2. And 3. Each version differs from the other. Version 2 is a more distinct version. It also has an edge that is thinner. The Oar Carver blade reference provides more details.
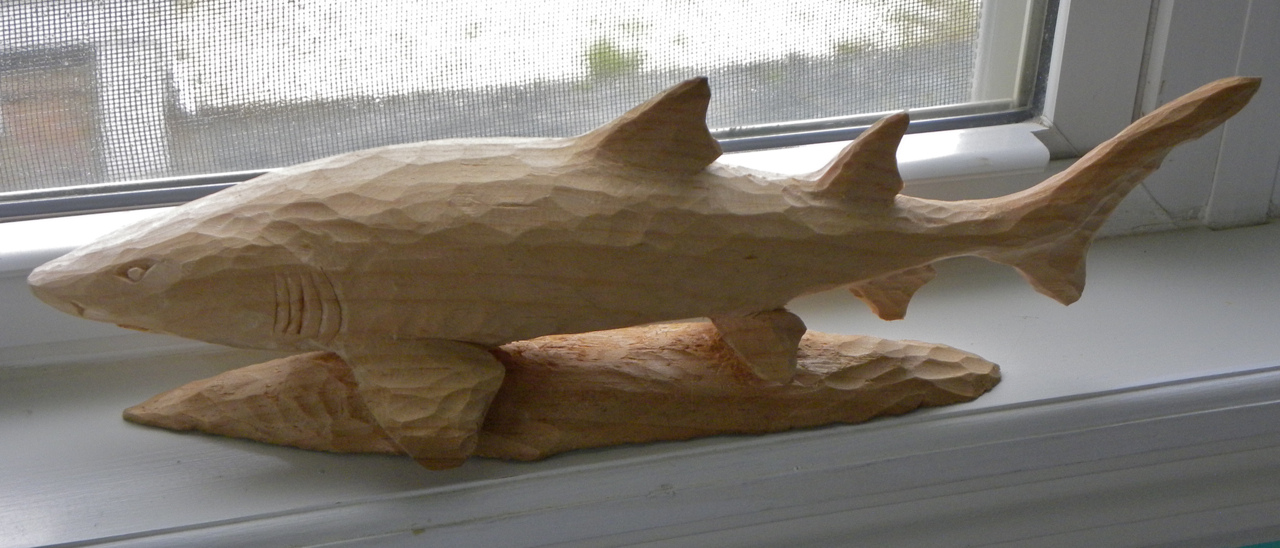
Mora produces two versions the 106 or 120. The Mora knife has a longer blade made from laminated steel. Both knives are simple and have an oval handle. They also come with a snap sheath. Another model, the Mora Frost 122 has a laminated steel blade and a 61 Rockwell high hardness. This knife is perfect for carving. The blade is also sharp and long-lasting.
Origins
The oar carving knife was created in Japan from ancient times. The handle is 4 1/2 inches long and the blade is solid hardwood. The oar has a long, flat blade, with a flat tip. The shaft of the knife is 53 inches long. The handle has been carved into a narrow circular shape, and the blade is separated from the shaft by a thin section made of wood.
Although the oar was the first known carving tool, its history is longer. The oar was first used to transport people along the coast and riverine. Because the Admiralty recognized the symbol easily and it was widely used, they chose the oar. Although the oar may have had different meanings, they are still useful. Listed below are some of its origins. If you are interested to learn more about the history behind knife-making, these are also very interesting.
FAQ
What is the difference between plywood and particle board?
Plywood is a combination of layers of wood, which are then pressed together under high pressure. Plywood comes with a range of thicknesses, and it is most commonly used for flooring and cabinets. Particle board is made up of sawdust mixed in resin, then compressed into large pieces. It's often used for home renovation projects. Both boards are strong and can be easily cut.
How do I determine what kind of wood my project is made from?
When purchasing wood, always check the label. The label should provide information about the wood species, moisture content, and whether preservatives have been used.
What's the difference between a hobbyist and a professional woodworker?
Hobbyists like making things with wood. Professionals focus more on quality. Hobbyists often take pride in the creations they make and often share them to family and friends. Professionals will spend hours researching designs and then begin to create a project. They will pay attention to every detail, from selecting the best materials to finishing the project perfectly.
Do you know anything more about woodworking?
It is easy for people to overlook the work involved in furniture making. Finding the right kind of wood is the most difficult part. There are so many options for wood, it can be difficult choosing the right one.
A problem is that wood doesn't have the same properties. Some woods will warp and others will split or crack. You must take these things into consideration before purchasing wood.
Does it take a genius to make woodworking work?
No. Woodworking does not require any special skills. Anyone can learn how to use basic power tools and techniques to create beautiful works of art.
How do you calculate woodworking prices?
It is essential to calculate costs as accurately as possible when pricing any project. It is important to ensure that you are getting the best materials prices. You should also consider other factors that could impact the cost of your project, such as experience, skill level, time, and money. You can find an estimate of the cost of different woodwork projects in our guide to common DIY tasks.
Statistics
- Most woodworkers agree that lumber moisture needs to be under 10% for building furniture. (woodandshop.com)
- In 2014, there were just over 237,000 jobs for all woodworkers, with other wood product manufacturing employing 23 percent; wood kitchen cabinets and countertop manufacturing employing 21 percent. (theartcareerproject.com)
- If your lumber isn't as dry as you would like when you purchase it (over 22% in Glen Huey's opinion…probably over 10-15% in my opinion), then it's a good idea to let it acclimate to your workshop for a couple of weeks. (woodandshop.com)
- The best-paid 10 percent make $76,000, while the lowest-paid 10 percent make $34,000. (zippia.com)
External Links
How To
How to drive a nail through wood
The first step in driving a nail into wood is to choose the correct size and type of hammer. There are many types of hammers that you will find: claw hammers and sledgehammers; mallets; ball peen hammers; and hatchets. Each type of hammer has its pros and cons. A claw hammer is best for hitting nails or hard objects. However, it can be difficult to pinpoint exactly where the blow will land. The sledgehammer works well for large areas, but is too heavy for smaller tasks.
Place your hand flat on the side of your chosen hammer so that the handle rests in your palm. You can grip the handle with your fingers, but not so tight that it causes injury. Hold the hammer straight up, keeping your wrist relaxed. You should then swing the hammer straight up, keeping your wrist relaxed. You should feel the impact of the hammer striking the nail. If you're having trouble getting the hang of swinging a hammer, practice with a block of wood until you get the rhythm down.
The hammer should be held close to your body when you are ready to begin driving the nail. You will need to position the nail so it is parallel to the wood. Keep your eyes on the tip. Swing the hammer forward, and then move the hammerhead. You can repeat this several times, increasing your swing speed. Once you have mastered this technique, increase the power of your swings. You can hold the hammer over your shoulder and forcefully bring it down. This way, you'll be able to put more energy behind your blows.
Once you have made the first hole, remove your hammer. To pull out the remaining nails, use a screwdriver or pry bar. You should ensure that the nails are flush with the board's surface to avoid splitting the wood.